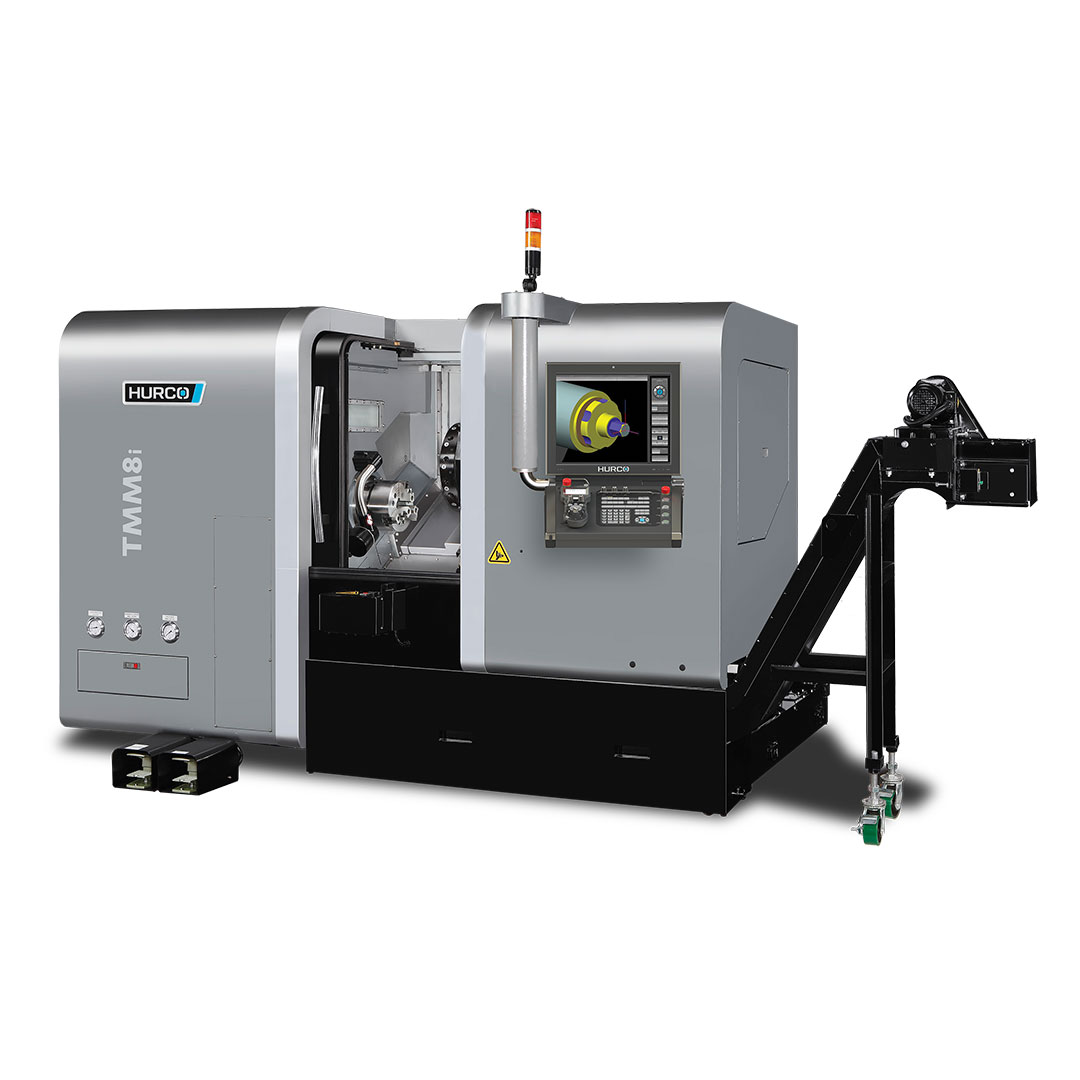
Montar un taller de metalmecánica es una excelente oportunidad para emprendedores y profesionales del sector industrial. Sin embargo, elegir las máquinas y herramientas adecuadas es un reto y no basta con tener experiencia técnica o una lista de clientes potenciales.
Muchos talleres fracasan o ven limitada su capacidad de producción por errores cometidos desde su planificación. Por eso, en este artículo abordamos los errores más comunes al montar un taller metalmecánico y cómo evitarlos, con un enfoque práctico para asegurar una inversión rentable, productiva y segura. Antes de emprender, toma en cuenta los siguientes puntos:
Elige la maquinaria adecuada y considera la distribución del espacio
El primer paso crítico es elegir las máquinas y herramientas. Muchos emprendedores adquieren equipos sin evaluar realmente el tipo de trabajos que realizarán, el volumen de producción o el espacio disponible en el taller. Esto puede traducirse en:
- Compra de máquinas sobredimensionadas o innecesarias.
- Equipos que no se ajustan a los materiales o procesos del taller.
- Espacios mal organizados, con obstáculos que entorpecen el trabajo.
Por ejemplo, incluir demasiadas máquinas de taller en un área pequeña puede crear cuellos de botella y aumentar el riesgo de accidentes.
Cómo evitarlo:
- Analiza qué procesos vas a realizar con mayor frecuencia (corte, torneado, soldadura, fresado, etc.).
- Prioriza la adquisición de máquinas y herramientas industriales versátiles y modulares.
- Diseña un plano de distribución del taller antes de instalar maquinaria, considerando zonas de paso, seguridad y ventilación.
Toma en cuenta el flujo de trabajo y la seguridad industrial
Un taller eficiente no solo depende de tener buenas máquinas, sino también de un flujo de trabajo lógico y seguro.
Si los materiales deben transportarse de un extremo a otro del taller sin orden, o si los operarios trabajan en espacios estrechos o mal iluminados, el resultado será pérdida de tiempo y aumento del riesgo de accidentes.
Además, la seguridad industrial muchas veces se deja en segundo plano, lo cual es un error grave. La falta de señalización, el mal almacenamiento de materiales y la ausencia de protocolos ante emergencias pueden derivar en incidentes que afecten al personal y al negocio.
Cómo evitarlo:
- Organiza el flujo de trabajo en sentido lineal o circular, para evitar desplazamientos innecesarios.
- Delimita zonas de riesgo (corte, soldadura, carga de materiales) con señalización visible.
- Asegúrate de que todo el personal utilice equipo de protección y que se realicen inspecciones periódicas a las máquinas y herramientas del taller.
Invierte en la tecnología adecuada
Una tentación frecuente es reducir la inversión inicial comprando equipos antiguos o de segunda mano. Aunque esto puede parecer una solución económica, muchas veces se convierte en una fuente constante de problemas:
- Máquinas menos precisas o lentas.
- Repuestos difíciles de conseguir.
- Mayor consumo de energía.
- Riesgo de fallas y paradas imprevistas.
En el entorno competitivo de la metalmecánica, contar con tecnología moderna no es un lujo, sino una necesidad para ofrecer calidad, rapidez y seguridad.
Cómo evitarlo:
- Investiga antes de comprar: compara modelos, consulta a proveedores confiables y analiza el costo de operación a largo plazo.
- Prioriza máquinas y herramientas con control digital (CNC), mejor eficiencia energética y disponibilidad de soporte técnico.
- Si compras equipos usados, asegúrate de que estén certificados y en condiciones óptimas de funcionamiento.
Capacita al personal en nuevas herramientas
Otro error común es subestimar la necesidad de capacitación técnica. Aunque el personal tenga experiencia en talleres, cada equipo tiene especificaciones propias, especialmente si hablamos de máquinas y herramientas industriales de nueva generación.
Operar maquinaria sin capacitación adecuada no solo reduce la productividad, sino que también aumenta el desgaste del equipo y los riesgos para el operador.
Además, la industria de la metalmecánica está en constante evolución: nuevos materiales, técnicas y tecnologías aparecen con frecuencia, y es necesario actualizarse.
Cómo evitarlo:
- Incluye en tu presupuesto inicial un plan de capacitación continua.
- Exige a los proveedores que incluyan formación técnica al instalar nuevas máquinas de taller.
- Motiva al personal a participar en cursos, seminarios y certificaciones relacionadas con el uso de máquinas y herramientas modernas.
Consejos adicionales para un taller metalmecánico exitoso
Además de evitar los errores mencionados, considera estas buenas prácticas:
1. Mantén un sistema de mantenimiento preventivo
La vida útil de tus máquinas y herramientas depende del mantenimiento regular. Programa revisiones, cambios de aceite, calibraciones y limpieza para evitar paradas imprevistas.
2. Establece controles de calidad
No basta con producir rápido; también debes producir bien. Implementa sistemas de control para asegurar tolerancias, acabados y resistencia según lo requerido.
3. Gestiona correctamente el inventario
El mal manejo de insumos y repuestos genera pérdidas. Usa un sistema de inventario para gestionar desde materias primas hasta herramientas menores.
4. Respeta la normativa legal y ambiental
Evita problemas legales cumpliendo con las normativas laborales, de seguridad y ambientales aplicables a talleres metalmecánicos.
Montar un taller de metalmecánica exitoso requiere más que una inversión en equipos. Es fundamental planificar cuidadosamente cada detalle: desde la selección de máquinas y herramientas, la distribución del espacio, el flujo de trabajo y la capacitación del personal, hasta la inversión tecnológica adecuada.
Evitar errores como la mala elección de maquinaria, ignorar la seguridad industrial o operar con tecnología obsoleta puede marcar la diferencia entre un negocio sostenible y uno condenado a perder eficiencia, calidad y rentabilidad.
Con una visión estratégica, el uso correcto de máquinas y herramientas industriales y un equipo capacitado, tu taller estará listo para competir en un sector exigente, pero lleno de oportunidades.
Conoce el catálogo que tenemos y contacta a nuestros asesores de Tecnomaquinaria para hacer la selección más adecuada de máquinas y herramientas para tu taller.