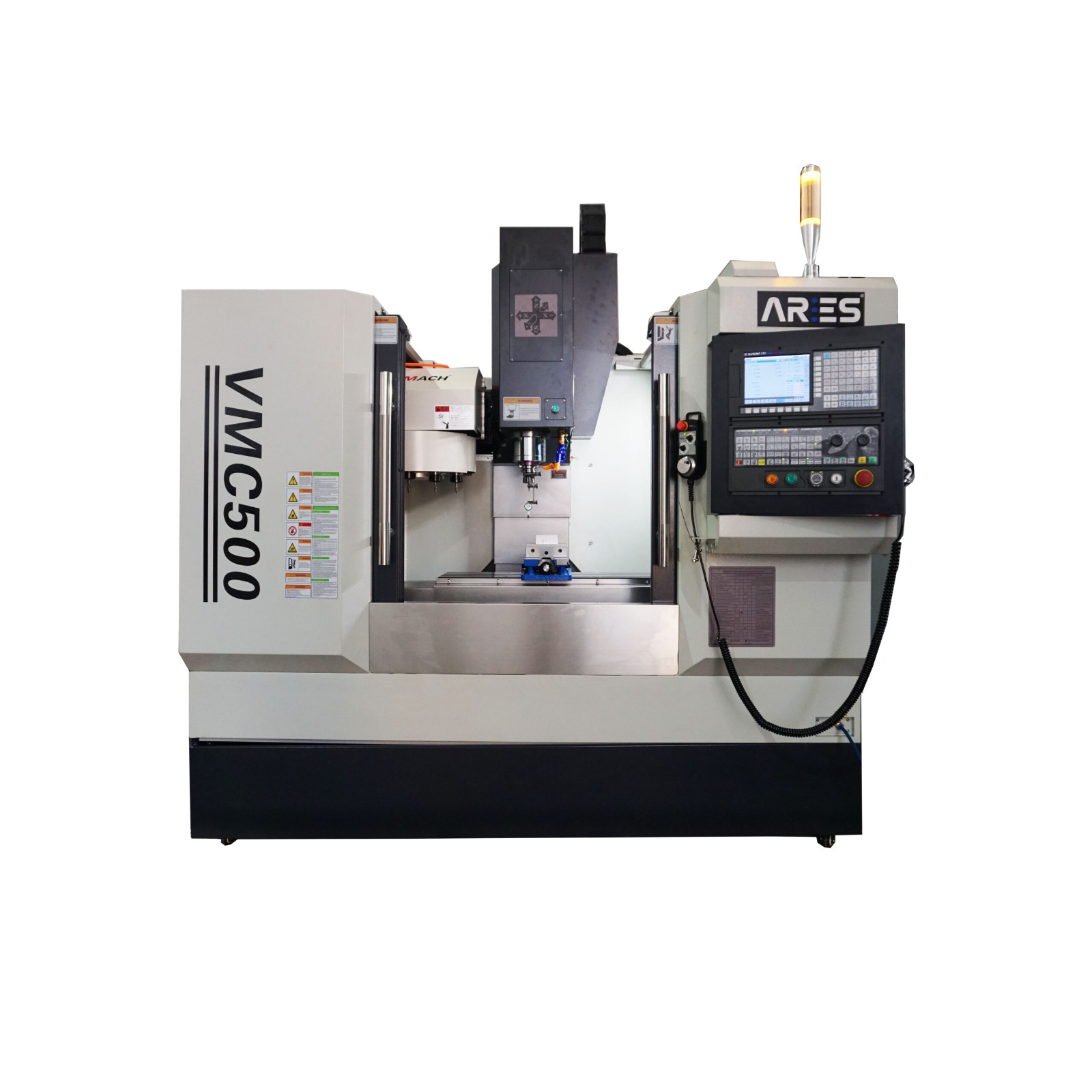
La elección adecuada de máquinas de taller es una de las decisiones más estratégicas para cualquier negocio del sector metalmecánico. Un taller industrial bien equipado puede incrementar la productividad, reducir errores, y facilitar el crecimiento a largo plazo.
Sin embargo, no todos los talleres tienen las mismas necesidades, por lo que seleccionar el equipo para taller industrial adecuado depende directamente del tipo y tamaño de producción.
En este artículo, analizaremos cómo deben equiparse los talleres pequeños y medianos, cómo evaluar la relación costo-beneficio al adquirir maquinaria, y cómo planificar un crecimiento escalable en el entorno de los talleres metalúrgicos y mecánicos.
Talleres pequeños vs. medianos: qué máquinas priorizar
Uno de los errores más comunes al montar un taller es querer adquirir todas las máquinas posibles desde el inicio. Esto no solo representa una inversión elevada, sino que puede comprometer el flujo de trabajo por falta de espacio o mantenimiento adecuado. Por eso, lo ideal es identificar el núcleo productivo del taller y elegir equipos que maximicen la eficiencia operativa desde el primer día.
¿Qué máquinas priorizar en un taller pequeño?
Un taller pequeño generalmente se enfoca en reparaciones, fabricación ligera o trabajos personalizados. En este escenario, la maquinaria básica para taller debe ofrecer versatilidad y ocupar el menor espacio posible. Estas son algunas opciones fundamentales:
- Torno mecánico básico: Ideal para piezas cilíndricas y trabajos de ajuste fino.
- Taladro de banco: Para perforaciones precisas en distintos materiales.
- Esmeriladora de banco: Fundamental para desbaste y acabado superficial.
- Soldadora MIG o TIG: Dependiendo del tipo de trabajo, permite uniones de alta calidad.
- Sierra de cinta o sierra sensitiva: Para cortes limpios en metal.
Además, los talleres metalúrgicos pequeños pueden aprovechar máquinas combinadas o equipos multipropósito para reducir costos iniciales sin sacrificar funcionalidad.
¿Y qué pasa con un taller mediano?
En un taller industrial mediano, el enfoque suele estar en la producción en serie, fabricación por encargo o mecanizado de mayor precisión. Aquí se puede invertir en maquinaria más especializada y robusta, como:
- Fresadora universal o CNC: Fundamental para operaciones complejas y trabajos repetitivos.
- Dobladora de lámina: Para piezas metálicas con formas específicas.
- Cizalla hidráulica: Para cortes rectos en placas gruesas o grandes volúmenes.
- Compresores industriales: Para alimentar sistemas neumáticos o herramientas de aire.
- Rectificadora: Para acabados finos en piezas de precisión.
En este tipo de taller, es recomendable separar áreas de trabajo (soldadura, mecanizado, corte) para optimizar los flujos de producción y garantizar la seguridad operativa.
Relación costo-beneficio en la selección de equipos industriales
Uno de los criterios clave al momento de adquirir equipo para taller industrial es la relación costo-beneficio. Comprar maquinaria no solo implica el gasto inicial, sino también mantenimiento, capacitación, consumo energético y compatibilidad con otros procesos.
¿Cómo evaluar esta relación?
- Frecuencia de uso: Una máquina que se usará a diario justifica una mayor inversión que una que se utilizará esporádicamente.
- Productividad esperada: Calcula cuántas piezas por hora puede procesar la máquina y cómo eso se traduce en ingresos.
- Consumo energético: Una máquina más eficiente energéticamente puede ahorrar dinero a largo plazo, aunque su precio inicial sea más alto.
- Costos de mantenimiento y repuestos: Equipos más populares suelen tener mejor disponibilidad de repuestos y técnicos especializados.
- Flexibilidad: Algunas máquinas ofrecen múltiples funciones, lo cual es ideal si tu producción varía con frecuencia.
Además, es importante considerar si se debe comprar maquinaria nueva o usada (link a la sección). Las máquinas usadas pueden representar un ahorro importante, pero es fundamental asegurarse de que estén en buen estado y cuenten con soporte técnico disponible.
Aunque la segunda opción es más cara, si su rendimiento permite duplicar la producción y reducir desperdicios, a mediano plazo ofrece una mejor relación costo-beneficio.
Crecimiento escalable en talleres metalmecánicos
La visión a futuro es esencial en cualquier taller metalúrgico o mecánico. Adquirir equipos pensando solo en el presente puede frenar el crecimiento y limitar la capacidad de asumir nuevos proyectos. En cambio, pensar en un modelo escalable permite crecer de forma ordenada y sostenible.
¿Cómo planificar un crecimiento escalable?
- Identifica tus procesos críticos: ¿Qué operaciones son el corazón de tu producción? Automatízalas o fortalece esas áreas primero.
- Invierte en infraestructura modular: Compra mesas de trabajo, bancos y herramientas que se puedan reubicar fácilmente.
- Deja espacio para máquinas futuras: Planea la distribución del taller considerando zonas de expansión o posibles mejoras.
- Establece alianzas con proveedores: Esto facilita el acceso a financiamiento o upgrades de maquinaria conforme crece la demanda.
- Capacita constantemente al personal: El equipo humano debe evolucionar junto con la tecnología para que el crecimiento sea efectivo.
Contar con las máquinas para taller mecánico adecuadas no solo determina la calidad de tus productos, sino también la rentabilidad de tu operación. Ya sea que administres un pequeño taller de mecanizado o estés desarrollando un taller metalúrgico con ambición de crecimiento, la clave está en elegir de forma inteligente, con base en tu tipo de producción y objetivos a futuro.
Evalúa siempre la relación costo-beneficio, prioriza la maquinaria básica para taller en etapas tempranas, y planifica un crecimiento escalable que te permita integrar nueva tecnología conforme tu negocio lo requiera.
Recuerda: un taller bien equipado no es el que tiene más máquinas, sino el que sabe sacar el máximo provecho de cada una de ellas.
En Tecnomaquinaria tenemos venta de maquinaria industrial, y una amplia gama de máquinas y herramientas para tu taller. Encuentra la tuya en nuestro catálogo y contáctanos para más información.