El equipo de corte y los equipos de grabado láser son muy útiles si se quieren crear diseños personalizados en diferentes materiales como: madera, metal, plástico, vidrio, cuero, tela, entre muchos otros. Esta maquinaria nos permite obtener una precisión muy elevada, calidad y rapidez en los proyectos de corte láser y grabado.
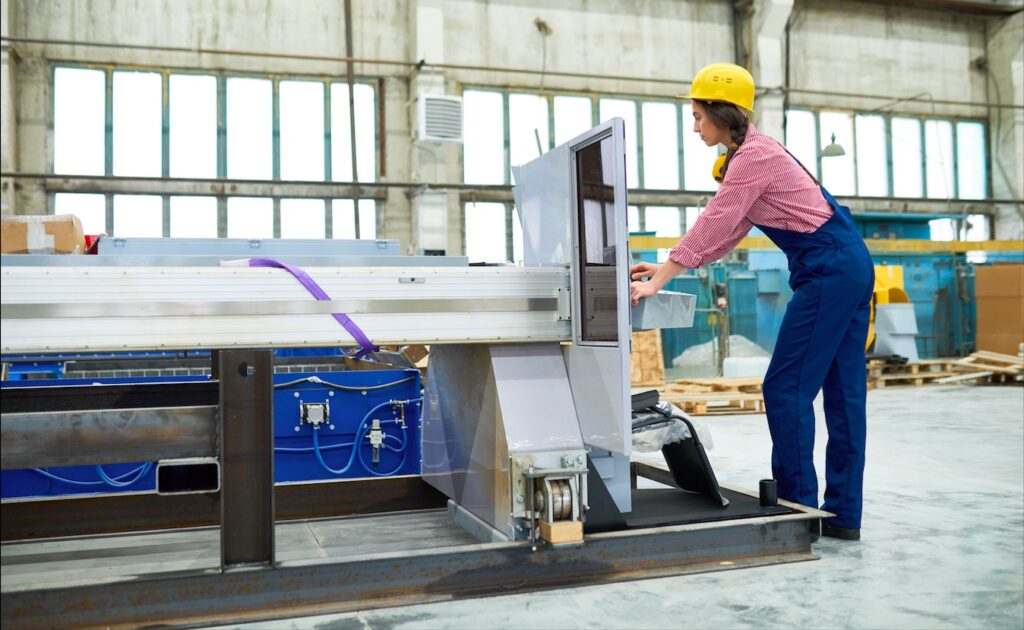
Maquinaria CNC: una introducción
Las máquinas CNC agilizan los procesos de manufactura en el sector metalmecánico, son máquinas muy eficaces, porque además se obtienen acabados de alta calidad y precisión. Estas máquinas están controladas por computadora, por lo que pueden realizar operaciones automáticas.
CNC significa Control Numérico por Computadora, esto se refiere al sistema que coordina los movimientos de los ejes de la máquina de acuerdo a los datos que recibe del software.
El software CAM (Computación aplicada a la fabricación) o CAD (Computación aplicada al diseño) le indica a la máquina CNC cómo cortar la materia prima de forma automática.
Primero, el software CAD hace un diseño 3D de la pieza que se quiere obtener. Después, el diseño 3D se pasa al software CAM, que crea un conjunto de instrucciones para la computadora (código G) que controla la secuencia de movimientos de las herramientas que cortan la pieza.
Este código G incluye las coordenadas de las partes específicas de la pieza, la herramienta requerida, las velocidades y avances adecuados y los comandos para activar y desactivar el líquido refrigerante.
La MCU (unidad de control de la máquina) convierte el código G en instrucciones para los motores y los husillos servo.
Siguiendo las instrucciones digitales, la máquina CNC mueve la herramienta de corte o la pieza en varios ejes para darle forma a la materia prima según lo deseado.
Para qué sirve una maquinaria láser CNC
Una maquinaria láser CNC es un tipo de máquina CNC que utiliza un haz de luz de alta intensidad para cortar o grabar materiales. El láser se genera en una fuente, se dirige a través de un sistema óptico y se enfoca en el punto de trabajo, donde se produce el corte o el grabado.
Una maquinaria laser CNC puede tener diferentes aplicaciones, dependiendo del tipo de láser, la potencia, el material y el diseño que se quiera realizar. Algunas de las aplicaciones más comunes son:
- Corte y grabado de piezas industriales, como engranajes, placa, tubos, etc.
- Corte y grabado de piezas artísticas, como joyas, trofeos, adornos, etc.
- Corte y grabado de piezas decorativas, como letreros, etiquetas, invitaciones, etc.
- Corte y grabado de piezas textiles, como ropa, calzado, bolsos, etc.
Equipos de corte y grabado láser
Los equipos de corte y grabado láser son herramientas muy versátiles que permiten realizar productos decorativos en gran cantidad.
La ventaja de estas máquinas es que pueden crear tus diseños en los programas que habitualmente usas y después cargarlos para que se realice el grabado. Existen diferentes tipos de equipos:
- Equipos de corte y grabado láser CO2: utilizan láser de dióxido de carbono, que se genera mediante una descarga eléctrica en una mezcla de gases. El láser de CO2 tiene una longitud de onda de 10.6 micrómetros, lo que lo hace adecuado para cortar y grabar materiales orgánicos, como madera, papel, cuero, tela, etc. Estos equipos puede tener una potencia de hasta 150W y una capacidad de trabajo de hasta 1300x900mm.
- Equipos de corte y grabado láser de fibra: El laser de estos equipos es de fibra óptica, se genera mediante un diodo láser que bombea una fibra dopada con iones de tierras raras. El láser de fibra tiene una longitud de onda de 1.06 micrómetros, lo que lo hace adecuado para cortar y grabar metales, como acero, aluminio, cobre, etc. Estos equipos pueden tener una potencia de hasta 6,000W y una capacidad de trabajo de hasta 3000 x 1500 mm.
- Equipos de corte y grabado láser YAG: Utilizan un láser de granate de itrio y aluminio dopado con neodimio, que se genera mediante un flash lámpara que bombea un cristal sólido. El láser YAG tiene una longitud de onda de 1.06 micrómetros, lo que lo hace adecuado para cortar y grabar metales y algunos materiales no metálicos, como cerámica, vidrio, etc. Estos equipos pueden tener una potencia de hasta 600 W y una capacidad de trabajo de hasta 600 x 600 mm.
Ideas de mantenimiento para tu equipo de corte
Para dar un buen mantenimiento a tu equipo de corte láser, es necesario que se realicen acciones periódicas como:
- Limpiar el sistema óptico: todos los días antes de poner a funcionar la máquina se recomienda hacer esta limpieza, siempre con la máquina apagada, se debe de ser sumamente cuidadosos para evitar que el lente se dañe, hacerlo de preferencia con un paño suave y líquido especial.
- Revisar sistema de refrigeración: El agua y el radiador mantienen la temperatura adecuada del láser, por ello hay que revisar el nivel y la calidad del agua, cambiarla cada tanto, esto evitará que se contamine o se evapore, lo que causaría un sobrecalentamiento o daño al láser. Así tu equipo de corte y el láser de tu máquina estarán óptimos.
- Ajustar el sistema de enfoque: Esto es, el cabezal y la boquilla que determinan la distancia entre el láser y el material. Es importante ajustar el sistema de enfoque según el tipo y el grosor del material, para lograr un corte o un grabado preciso y uniforme.
Contáctanos si buscas saber más acerca de este tipo de maquinaria industrial o consultar sobre cualquier tipo de mantenimiento sobre tu equipo de corte o grabado láser. En Tecnomaquinaria, podemos asesorarte para que tengas al alcance las herramientas que tu negocio requiere.